Resultados
Soluções produtivas
Os objetivos propostos pelo projeto foram cumpridos em todos os domínios especificados inicialmente, respectivamente no desenvolvimento e aplicação de uma "metodologia integrada de desenvolvimento e qualificação de aeroestruturas" denominada de "better design", demonstrável através da redução de custos e peso do "demonstrador aplicado a uma estrutura periférica integradora de tecnologia de fabrico estudada". Contudo, também foi verificado a construção do "demonstrador representando uma estrutura de controlo / sustentadora" integradora das tecnologias e sistemas selecionados, posteriormente ensaiado com recurso ao "demonstrador da metodologia de ensaios".
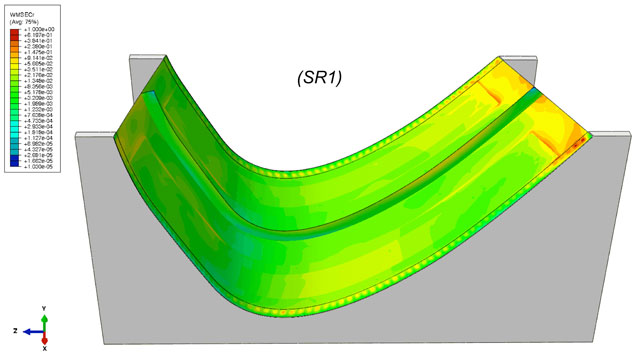
Redução de custos
Em termos de redução dos custos de fabrico, obteve-se um resultado superior a 15%, quando comparado a construção por infusão em vácuo com o processo tradicional por autoclave, comumente utilizado na indústria aeronáutica. Os resultados obtidos estão associados à aplicação de técnicas de fabrico por infusão a vácuo que permitem não só processos mais económicos, mas também eliminação de materiais anteriormente usados. A capacidade de integração de componentes distintos um único só é possível devido às técnicas de produção por infusão a vácuo resultando na redução de componentes necessários produzir assim como redução de hardware. Desta forma a redução dos custos é verificável através da redução dos custos inerentes ao desenvolvimento e produção como é exemplo os custos de desenvolvimento de desenhos CAD, custos de produção associados aos moldes (por norma em alumínio), de hardware (como é exemplo a utilização de rebites), montagem e inspecção requeridas.
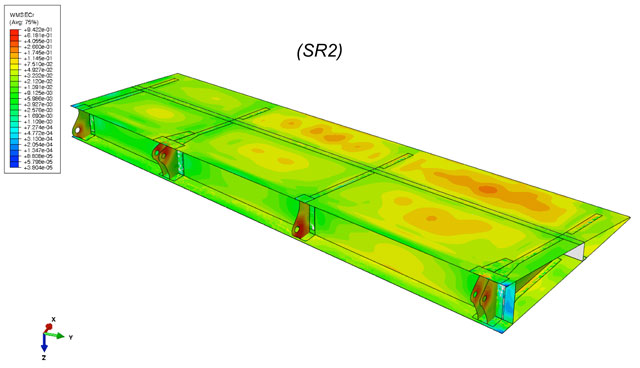
Processo de desenvolvimento
A eficácia do processo de desenvolvimento resultou na execução de 2 iterações. Numa primeira fase foram realizados ensaios coupon na qual os resultados auferidos permitiram o desenvolvimento da subestrutura periférica e respectivo banco de ensaios. Numa segunda fase os conhecimentos adquiridos durante o desenvolvimento do banco de ensaios da subestrutura periférica assim como durante os ensaios, permitiram implementar melhorias no desenvolvimento da subestrutura sustentadora / controlo, respectivo banco de ensaios e execução de ensaio.
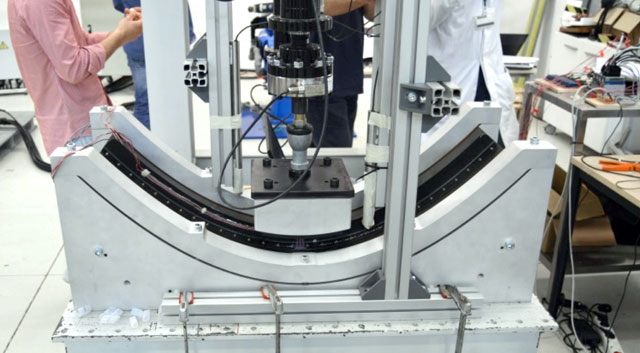
Tempo de qualificação
Para o tempo de qualificação, foram realizadas as tarefas de montagem, ensaios e relatórios das análises e resultados, com uma excelente otimização dos tempos previstos para cada uma delas. Desta forma, o tempo de montagem dos bancos de ensaio foi reduzido para 1 mês, em parte devido não só ao uso de métodos virtuais de montagem, mas também ao uso de estruturas modulares. Os ensaios decorreram durante 5 meses, período menor do que os 12,75 meses previstos, devido às metodologias adoptadas assim como o recurso à ferramenta de SHM reduzindo desta forma o tempo de inspeções. Quanto aos relatórios, estes viram o seu tempo de realização encurtado para 12 dias, recorrendo ao uso das metodologias de concurrent engineering e better design. Conclui-se portanto, que o tempo total foi eficazmente diminuído, passando dos 12,75 meses previstos para 7 meses, fato possível também devido à elevada interação entre as equipas, com a realização de reuniões constantes, antecipando problemas e implantando soluções.
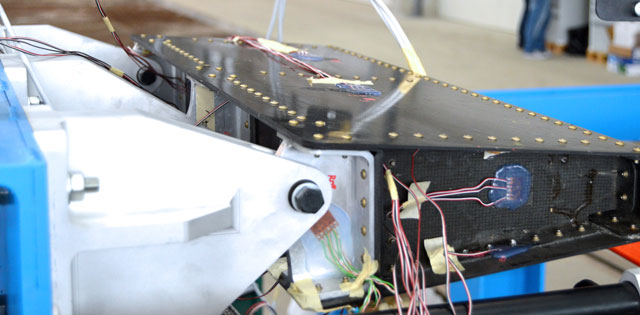